Busway Electrification Systems for Movable Trolley Service
General Information:
Feedrail® systems are capable of providing multi-purpose trolleys or stationary plug-ins for installations requiring a source of electrical power which can be reconfigured without rewiring.
These systems provide moveable outlets for electrical power along their entire length. The systems are especially suited for use where conventional wire systems would be cumbersome and costly.
Plug-in Jacks with stationary power take-offs, are available for all Feedrail® systems.
The busway-supported outlets called “trolleys” (Feedrail® 60 system only) make contact with the enclosed bus bars and provide a continuous moveable connection for electrical devices. The trolleys are easily inserted and removed through door-busway sections.
As additional outlets are needed, trolleys (Feedrail® 60 System only) or stationary plug-ins can be quickly and efficiently inserted, their numbers being limited only by the current-carrying capacity of the busway and the capacity of each outlet.
Reliable design assures uniform contact pressure, limiting work stoppages due to electrical and mechanical interruptions in supplying power.
Advantages of these systems include low installation costs with complete re-usability; ease of adding outlets as required; electrical and personnel safety; compactness; dependability and minimum maintenance expense.
All “busway (track) sections” are factory assembled for ease in handling and rapid installation. No special tools are required.
Systems are designed for indoor use in non-hazardous, non-corrosive, dry atmosphere.
|
Basic Information:
- 60 Amps Continuous
- 90 Amps Intermittent
- Trolleys Rated at 15 or 30 Amps Continuous
- 300 Volts (4 or 5 pole systems); 60 Volts (2, 3 or 4 pole systems)
- Made in the U.S.A.
More Information:
|
UL & CSA Listed
Feedrail® is listed by Underwriter’s Laboratories, Inc. (U.L.) under BUSWAYS AND ASSOCIATED FITTINGS (File E11348 for Feedrail® / File E165922 for Electro-Rail® ) and as a CRANE AND HOIST ELECTRIFICATION SYSTEM (File E31188 for Feedrail® ). Feedrail® is also listed by the Canadian Standards Association (C.S.A.) under WIREWAYS AND BUSWAYS (File LL-7907 for Feedrail® / File LL 103287-1 for Electro-Rail® ).
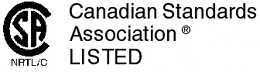
Track Supports
Steel clamp type track hangers for supporting track sections from strap or rod. Additional track hangers can be attached at intermediate points.
Track
Track sections consist of a brake press welded two-piece 13-gauge zinc coated steel housing and the enclosed current carrying bus bars and insulators, all factory assembled in convenient lengths ready for easy, fool-proof installation on the job. The lower horizontal portions of the houseing serve as smooth, rigid runway sfor the trolleys.
“Multi-Conductor track sections are available in various types — Plain, Door, Feed, Sectionalizing, Transfer, Curved and Expansion Track sections.
Bus bars are of hard drawn copper. They are amply proportioned to carry the specified current of 60 amperes per pole continuoulsly, 90 amperes per pole intermittently, without overheating. Bus bar connectors assure full current carrying capacity across the joints without interfering with the free travel of the trolley contacts.
Insulators are made of a high insulating and arc-resistent material. They are held on 12” centers by the casing.
Trolleys
Feedrail® trolleys are designed to provide stable clean power; arcing and hot spots are essentially eliminated. Stable clean power is required for trouble free operation of today’s computer controlled equipment and machinery.
Trolleys are available in fusible and non-fusible types.
Basically, all Feedrail® “Multi-Conducotr” trolleys have a chassis-insulator-contact assembly. The chassis is of heavy gauge steel. The trolley wheels and guide wheels are of the ball-bearing type. A substantially proportioned insulator block combines the best insulating properties with high are resistance.
Feedrail® “Multi-Conductor” trolleys are furnished with COPPER GRAPHITE BRUSH CONTACTS for movement up to 250 feet per minute. For rate of travel or conditions other than above, please consult factory.
A polarizing tab on the chassis, operating in conjunction with a stop in the door track section, permits insertion of the trolleys only one way. Equipment grounding may be made through the trolleys. Weights in excess of 40 pounds per trolley are not recommended.
Grounding
For the safety of personnel, the track casings of the Feedrail® system may be used as an equipment grounding conductor for grounding equipment through the individula trolleys.
Equpment grounding may be made by using the screw on the underside of the trolley chassis or on trolleys having bainets or boxes by using the grounding screw within the box. Track housing must be grounded through consuit or other suitable means.
Feedrail® “Multi-Conductor” systems are desinged for indoor service in essentially dry locations. Feedrail® systems areelectrified tracks in which the current carrying components are nclosed in protective steel housings. Smooth riding internally track-supported trolleys take off current and provide electrical power for crane and hoist or other types of electrification systems.
Feedrail® “Multi-Conductor” systems have been specifiacally developed to provide safe electrification for crane bridges, monorail-hoist installations, test lines, machine tools and similar applications.
The Feedrail"Multi-Conductor” systems are made up of standardized units, factory assembled for fast, complete installation without on-site fabrications.
Feedrail® “Multi-Conductor” systems may be used to provide both power and control. They are ideally suited for use on control circuits where other standard Feedrail® systems supply heavier electrification requirements.
CLOSE
1. Track sections are furnished with two track connecting bars at one end. Place sections end to end so that sections with and without connectors are facing.
|
2. Install Bus Bar Connectors on bus bars. Bring sections together, lining up threaded holes in connecting bars with the holes in the bottom of the track housing. Tighten connecting bar fastening screws to 25 inch-pounds torque. Slide ends of bus bars into unattached ends of bus bar connectors. Bring bus bars together, aligning ends of bus bars in section being installed with end of the track housing, shifting bus bars slightly if necessary (up to o inch gap may be left in bus bar joint to permit this alignment).
|
3. Install coupling plates into slots under top edges of the track housing. Bolt plates together.
|
4. Track sections can now be supported anywhere along the length of the section as is shown above. (Two hangers should be used per each track section).
|
CLOSE
1. Connect track sections as outlined in steps 1 and 2 on page 39. Then install coupling plate (cat. no. FX102).
|
2. Align holes in coupling plate with holes in top of the track section. As bolts are tightened, coupling plate will conform to the shape of the track. Support curved track sections with Auxiliary Hanger FR140 and clevis support FR105, in holes provided in top of track casing.
|
CLOSE
1. Mount bus bar terminal spacer by inserting prongs into ends of bus bar connectors as far as they will go and tighten screws securely. Align side plates into slots under top edges of the track housing at end of track. Bring plates together and fasten bolts securely.
|
2. Place end cap in position with trolley stop at bottom. Insert and fasten the two mounting screws on each side.
|
CLOSE
1. If bus bar connectors are on end of track, remove and keep them for use with dead end cap at other end of the track run. Set terminal spacer onto bus bars. Slip end feed connectors (having halflength slot in bottom) onto ends of bus bars and tighten screws securely.
|
2. Fasten side plates into slots under top edges of track casing, tighten securely. Remove knockout in feedbox frame to provide proper size hole for conduit. Attach box frame to side plates.
|
3. Mount box cover. When ready to connect power, remove cover, bring in conduit through hole in box frame, make wire connection to the end feed terminal lugs and replace cover.
|
CLOSE
1. Mount bus bar terminal spacer by inserting prongs into ends of bus bar connectors as far as they will go and tighten screws securely. Align side plates into slots under top edges of the track housing at end of track. Bring plates together and fasten bolts securely.
|
2. When ready to connect to power, bring in conduit through hole in box frame and make connection to terminal lugs. Replace side covers.
|
CLOSE
Feedrail® Multi-Conductor transfer track sections are similar to Plain Track sections except that one or both ends are flared and have a tapered insulator serving as a guide for entrance of the trolleys.
On installations having transfer points, (*turntables, slide or tongue switches, etc.) the Transfer Track sections should be installed first so that proper gaps can be set. These gaps between Transfer Track sections should not exceed b inch. (Transfer Track sections for use on turntables, slide or tongue switches, are not stock items but are manufactured specifically to conform to given dimensions.)
Where motor propelled hoists are used on runs which include transfer points, it is necessary to use two electrically inter-connected trolleys. The two trolleys must be spaced sufficiently so that current is maintained to one trolley while the other crosses the transfer point. Duplex Transfer Type Trolleys are designed particularly for this application.
Transfer Track sections at transfer points must be aligned accurately, both horizontally and vertically. They must be supported at the transfer ends by an FX-197 Transfer Point Hanger Set. (Hook bottoms of Transfer Point Hanger Set into slots in the under edges of the track housing. Bring the plates together and fasten to support with bolts as shown.)
In every case the mounting of Transfer Track sections should be designed to insure a rigid installation. They should be sway braced to maintain alignment.
Sections are installed and coupled to adjoining track sections.
CLOSE
Sectionalizing Track sections are used to electrically isolate parts of a track run while permitting movement of the trolleys through that portion of the track. All Sectionalizing Track sections are coupled in the same manner as Plain Track, shown on page 39. Note: The standard sections described on page 33 have internal insulators of a size which do not prevent the interrupting of the current to the trolley. The current is not only maintained through the trolley but the circuits on both sides are electrically tied together through the trolley contacts as the trolley passes the sectionalizing insulator. Other special sectionalizing track sections which are used in particular applications do break the current to the trolley. In these cases, two electrically connected trolleys must be used. They must be spaced sufficiently apart so that the contacts of one will be on the bus bars while the contacts of the other are passing the insulator. Unless connected in this manner, power will not be maintained to the trolley contacts as they cross the insulators and arcing at the trolley contacts will occur. Sectionalizing track sections must not be used as a circuit interrupting device.
CLOSE
At least one Expansion Track section should be installed in each 400 ft. of track run to compensate for the cumulative differences in expansion and contraction between the steel casings and copper bus bars. Additional Expansion Track sections may be required if the installation is subjected to a wide range of temperature changes.
Expansion Track sections must be used wherever an installation is made across a building or structural expansion joint.
The standard 10' Expansion Track section is designed to provide 2" of expansion and 2" of contraction above and below the normal 10' length, at 75°F. At the time of installation, the length of the Expansion Track section must be set in accordance with the table below.
When used at points other than a building or structural expansion joint to compensate for unequal expansion or contraction between the steel track housing and copper bus bars, support the Expansion Track section by the coupling plates at each end and by the center support plates from suitable support brackets.
When used across a building expansion joint, center the Expansion Track section across the building expansion joint and support at each end from coupling plates and from the center support plates. Center support must be on the same side of the building expansion joint as the side of the expansion section stenciled "STATIONARY."
Length Settings for Standard 10' Expansion Track
|
Installation Temperature
|
Distance in Feet *
|
100
|
200
|
400
|
100°F
|
9'11-3/16"
|
9'11-5/8"
|
9'11-1/4"
|
75°F
|
10'
|
10'
|
10'
|
50°F
|
10'3/16"
|
10'3/8"
|
10'3/4"
|
25°F
|
10'3/8"
|
10'3/4"
|
10'1-1/2"
|
* Distance Represents: (1) Footage between expansion track sections on installation having more than one expansion track section. (2) Overall length of run on installation having only one expansion track section.
|
CLOSE
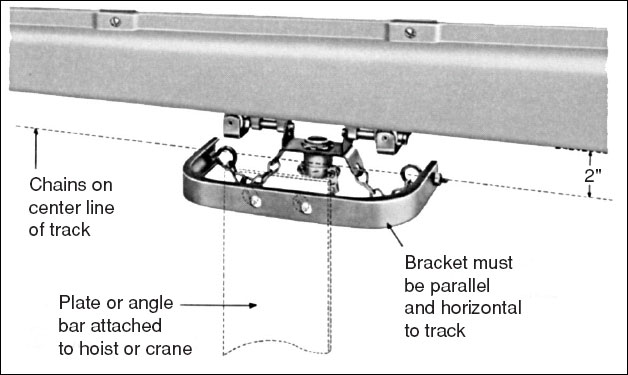
All trolleys must be pulled in such a manner that no strain is placed on the trolley by the pulling arrangement or electrical cable. A bracket and chain linkage, as shown, is recommended. Brackets must be attached to the hoist, crane bridge or other equipment so the chains are on the center line of the track and the bracket parallel to and 2" below the track. Flexible rubber covered cables must be used for electrical connection of each trolley.
CLOSE
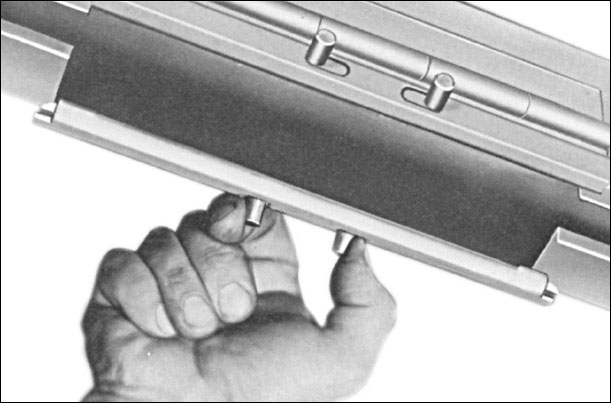
1. Press pins together on underside of door section and swing door open.
|
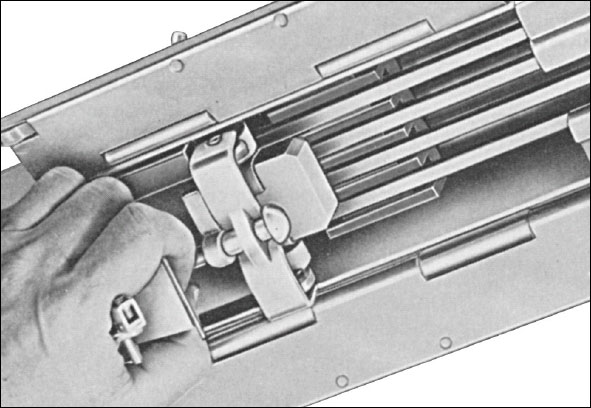
2. Insert trolley as shown. If trolley hits polarizing stop, remove, reverse 180° and reinsert. Close track doors.
|
CLOSE
Before a Feedrail® Multi-Conductor system can be planned or an estimate of the cost prepared, the electrical and mechanical requirements that the system must meet should be known. The following outlines list the basic data needed for all applications and the additional data required for various specific applications.
Basic For All
- Describe in detail the purpose for which the Feedrail® “Multi-Conductor” will be used. Will it be used with existing equipment?
- How many conductors will be required?
- What voltage and current is to be applied to each conductor? Where is the power source located?
- Details about any special requirements or conditions which the installation must meet such as moisture, corrosive fumes, high or low temperatures, etc.
For Electric Cranes
- Sketch giving number, location, length of crane runways and length of bridge. Show location of building expansion joints or expansion joints in the structure from which the Feedrail® will be supported.
- How many conductors will be required on each bridge run? How many for power? For control? How much current must each conductor carry?
- What is the maximum travel speed of the bridge? of the hoist?
- List of the crane’s motors — main hoist, auxiliary hoist, bridge travel, trolley travel— giving the type (D.C., wound rotor, squirrel cage, etc.) of each motor and its horsepower and full-load ampere rating.
For Electric Hoists
- Plan view sketch of the rail system on which the hoists will travel, giving the length of run, of straight sections, radii of any curves and dimensions of any switches. What is the minimum distance from Feedrail® to monorail in order to clear hoist? Show location of building expansion joints or expansion joints in the structure from which the Feedrail® will be supported.
- How many hoists will be used and what is the horsepower and full load current rating of each? Include horsepower and full load current rating of travel motors of any of the hoists that are motor propelled. What are the maximum travel speeds?
For Moving Test Lines
- Plan view sketch with dimensions showing the length of straight sections and radii of any curves, indicate the number of outlets required. If there are any sections along the run where test current will not be required, indicate their location and extent.
- What type of equipment will be tested.
- Give weight of units to be supported by the system.
- What amperage range and what fusing arrangements will be required?
For Production Machines
- Plan view sketch with dimensions showing the location of the Feedrail® system.
- Indicate the number of conductors required and give voltage and amperage requirements of each. Give horsepower and full load current rating of each motor.
- List any other equipment that will be powered by the Feedrail® and give its full load current rating.
For Special Requirements
- Plan view sketch with all dimensions which are necessary to make clear the location and extent of the Feedrail® “100” system and the radii of any curves it may contain. Show the location of the power source.
- Full details about equipment which will be operated from the system, including :
- Horsepower and full-load current rating of any electrical motors.
- Weight of any equipment to be supported by the system.
- Fusing arrangements required.
- Number of outlets needed.
Engineering Cooperation
Working out the details of a Feedrail® Multi- Conductor installation is not difficult once all the electrical and mechanical requirements have been definitely determined.
CLOSE
At all times Feedrail® equipment should be so protected and maintained as to be kept clean and dry.
Before the Feedrail® system is placed in operation, it should be thoroughly checked for horizontal and vertical alignment, adequate track support and free movement of trolley travel throughout the entire track run. All track, bus bar and feed connections should be mechanically tight. The system should be checked for possible grounds or short circuits. Any paint, grease, or other foreign matter accumulated during construction should be removed from the bus bars, insulation and track interior. Blow out all dust and other loose particles from inside the track.
Expansion sections, when used, must be properly adjusted, located and supported in accordance with installation instructions. Check bus bars and casing for accurate alignment.
Feedrail® is both an electrical and a moving mechanical system and therefore should be included as a part of your Preventive Maintenance Program.
Electrical Maintenance requires:
- Keeping the system dry and clean to prevent electrical leakage or “shorts” across the insulation.
- Maintaining electrical continuity by keeping bus bar contact surfaces clean and joints tight.
Mechanical Maintenance requires:
- Preventing excessive wear.
- Replacing parts showing excessive wear.
The following Preventive Maintenance procedure, periodically performed, is recommended:
- Remove, thoroughly clean all trolleys and lubricate the wheels. Feedrail® recommends Grade #1 Bearing Grease. This is softer grease than #2 and allows the grease to penetrate the bearings easier. Inspect contacts for excessive wear. Replace worn wheels and contacts.
- Clean bus bars with Feedrail® Bus Bar Cleaner.
- Blow out all foreign particles which have accumulated inside the track.
- Check trolleys for free movement within the track.
- Check all track supports, track joints, bus bar and feed connections for tightness.
This procedure should be repeated at regular intervals, consistent with the severity of the operations and usage of the system. Plants operating two or three shifts will require more frequent inspection of the Feedrail® equipment.
Feedrail® is not normally recommended for installations subject to vibration, frequent electrical overload, corrosive fumes and other abnormal conditions. However, should such conditions exist, more frequent inspections and maintenance will be required.
Before additional electrical loads are added to the system it should be determined that sufficient capacity is available.
CLOSE
The Trolley Busway System (Crane and Hoist Electrification System) shall be of metal enclosed type with internally tracksupported trolleys as manufactured by:
Genuine Feedrail®
Industrial Products
The System shall have a voltage rating (600)(300) Volts A.C., or (300)(250) Volts D.C. (2 pole) (3 pole) (4 pole) (5 pole), and a continuous current carrying capacity of 60 Amperes per Pole. (When used as a Crane and Hoist Electrification System, the System shall be rated at 60 Amperes continuous service and 90 Amperes intermittent service). The full current carrying capacity of the system shall be maintained throughout.
The System shall permit longitudinal movement of the housings and bus bars, independent of each other, in order to allow for unequal expansion and contraction as a result of temperature changes.
The System shall consist of standardized, interchangeable, Feedrail® units — track sections, coupling sets, dead end caps, track hangers and power takeoff trolleys, as called for on the plans.
Track sections shall be two-piece, 13 gauge, brake pressed, zinc-coated sheet steel enclosures having a continuous slot in the bottom and a heavy double webbed rib in the top. Rolled or drawn copper bus bars, capable of carrying 60 Amperes per pole continuously without overheating, shall be mounted within the steel enclosure on arc-resistant insulators.
Door track sections shall include two hinged doors in the bottom for insertion and removal of trolleys. Door openings shall have a mechanical polarization to insure proper polarity of the trolleys.
Track supported trolleys shall be Cat. No.__________________________ as listed in the Feedrail® Catalog. They shall have a zinc-plated sheet steel chassis with metal wheels for support. Horizontal guide wheels shall run in the slot of the Feedrail® track to prevent slewing and maintain alignment. Spring-loaded (roller) (or) (brush) contacts shall be mounted on arc-resistant insulation. When inserted in Feedrail® track, the contacts shall align with the bus bars at all times.
Trolleys shall be mechanically polarized with respect to door track sections.
CLOSE
As an aid in planning mountings, the basic dimensions of the Feedrail® ‘Multi-Conductor’ systems are shown below. These are offered as a guide only.
Mounting Methods
Examples of the methods commonly used for mountiing Feedrail® ‘Multi-Conductor’ systems track runs are shown below. These methods can be used in existing plants as well as in new buildings. Engineers and contractors will readily be able to devise other methods to suit special installations. In every case the mounting should be designed to insure a rigid installation in both horizontal and vertical alignment.
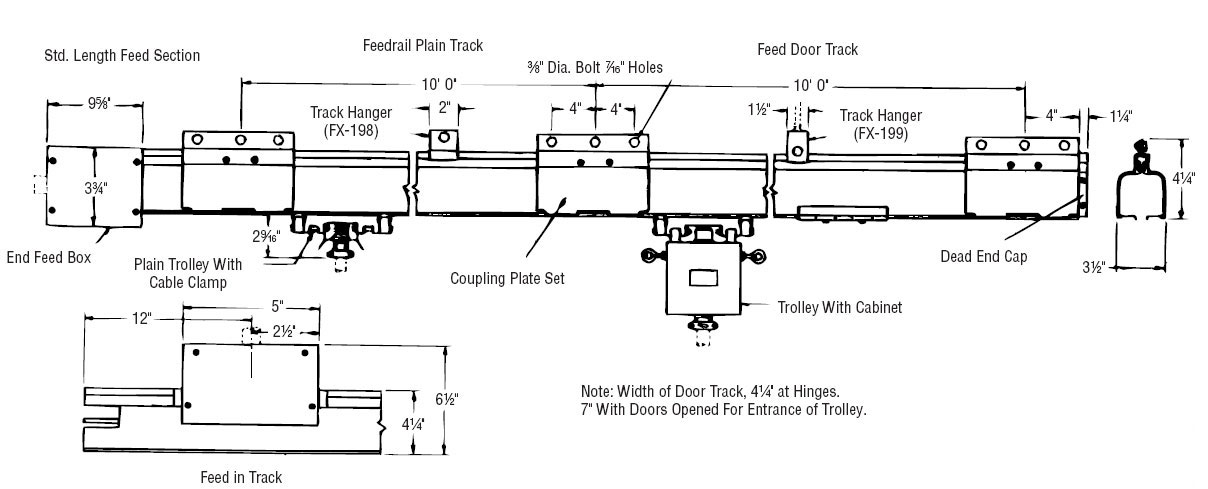
CLOSE
All of the components you'll need to build a brand new Feedrail FM or FX Series system have been organized below by category. It is recommended that you start with Track Sections and work your way through each category in the order they're presented. If you have any questions, please contact us and one of our highly trained Feedrail specialists will respond shortly.
All components, parts and accessories for the Feedrail FM and FX Multi-Conductor Trolley Series System can be found below. Use the product filter menu to narrow your search.
Trolleys
Feedrail® trolleys are designed to provide stable clean power; arcing and hot spots are essentially eliminated. Stable clean power is required for trouble free operation of today's computer controlled equipment and machinery. To learn more about FM & FX Multi-Conductor Series trolleys, click here.
Superior Design and Construction
The same efficient engineering and cleanout consturction which is a hallmark of the entire Feedrail system is evident in the internally track supported "Multi-Conductor" trolleys.
The chassis of these trolleys is of one-piece heavy gauge steel. It is equipped with heavy duty ball-bearing wheels for support; horizontally mounted ball-bearings guide wheels running in the slot of the track to prevent slewing; and ball-bearing wheels on pivoted arms of the undercarriage to prevent upthrust. This wheel combination assures smooth, easy running trolleys.
A polarizing tab is on the chassis. This, operating in conjunction with a stop at the door track opening, prevents insertion of the trolleys in improper polarity. A bumper is attached to each end of the chassis.
The insulator-contact assembly consists of a substancially proportioned mechanically strong arc-resisting insulator block on which the contact brushes are mounted and held in true alignment. Spring keep the brushes in continuous firm contact with the bus bars. The insulator-contat assembly is fastened to the chassis by machine screws and can be removed as a unit.
Feedrail "Multi-Conductor" trolleys are furnished with Copper Graphite Brush Contacts for movement up to 250 feet per minute and on all track runs, including curved track sections. Trolleys have crimp type connectors. A cable clamp is provided. Trolleys are available with or without pulling bracket and chain linkage. Equipment ground is provided on al trolleys. Standard trolleys are available in fusible and non-fusible types; transfer trolleys are of no-fusible type, eiher single or duplex. Transfer type trolleys are especially designed to facilitate crossing of gaps between crane bridges and spur runs or between slide switch sections and the main run. Where motor propelled hoists are used on runs which include transfer points, duplex type transfer trolleys must be used to insure continuous current while crossing the transfer points.
For rate of travel conditions other than below, consult technical service group.
Current Carrying Capacity:
Continuous current reating 15 and 30 Amperes
Voltage:
600 Volts A.C. or 250 Volts D.C. No Fusible, 2,3 or 4 pole
600 Volts A.C. or 250 Volts D.C. Fusible, 2, 3 or 4 pole
300 Volts A.C. or D.C. Non Fusible, 4 or 5 pole
250 Volts A.C. or D.C. Fusible, 4 or 5 Pole
Note: Amperage is for continuous load. Trolley contacts should not be used to make or break power to electrical load.
Note: Fusible Trolleys take 13/16" x 5" Cartidge Type Fuses. (Fuses not included)
CLOSE